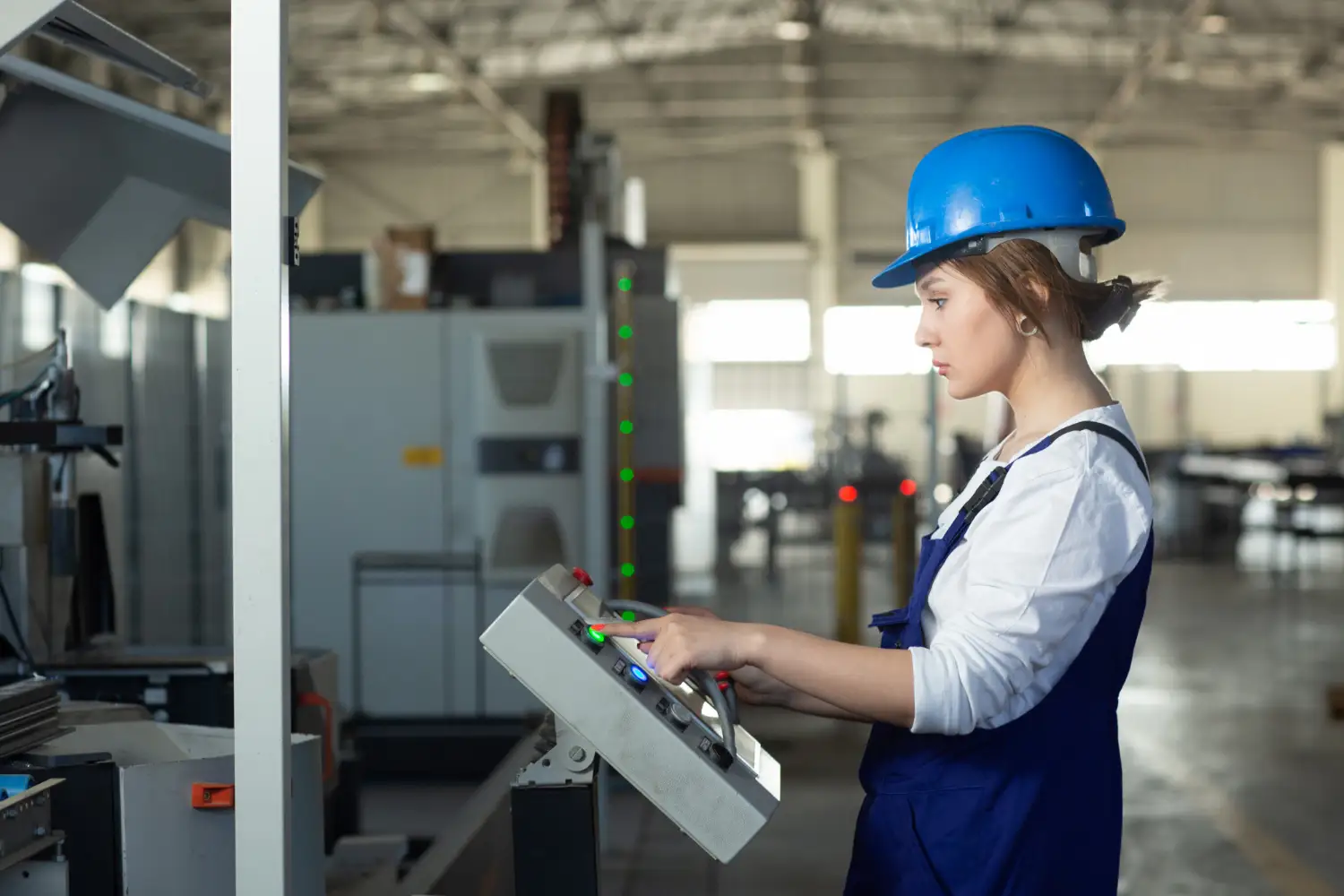
Je me permets de vous partager certaines situations rencontrées récemment chez nos clients. Il s’agit principalement du manque d’efficience des lignes de production, notamment des équipements de production, mais aussi de l’état d’esprit dans lequel ces machines ont probablement été conçues.
Les indicateurs de performance sont éloquents :
- Faible TRS (moins de 50 %),
- Taux de disponibilité insuffisant,
- MTBF insatisfaisant,
- Flexibilité très réduite,
- Taux de service faible,
- Charge mentale élevée,
- Pénibilité des postes aggravée par la forte variabilité induite par les dysfonctionnements machines.
En résumé, ces lignes et machines ne répondent pas aux exigences clients en termes de qualité, quantité et délais. De plus, elles engendrent des coûts de maintenance élevés, impactent la qualité et, dans certains cas, occasionnent des pertes matières significatives, notamment dans l’agroalimentaire.
La direction industrielle persiste souvent à imposer l’utilisation de ces machines, pensant ainsi les rentabiliser tout en essayant de satisfaire la demande client. Pourtant, les indicateurs et relevés de données sont alarmants et explicites. Il est compréhensible que lorsqu’une ligne ou une machine coûte plus de 3 millions d’euros, il soit difficile d’accepter de ne pas l’exploiter pleinement.
Ces situations ne sont malheureusement pas isolées et concernent souvent des machines spéciales, voire des prototypes (conceptions uniques) censés atteindre des capacités et cadences de production particulières. L’idée sous-jacente est qu’une ligne intégrant des machines complexes, limitant le travail manuel, sera plus performante. Ce paradigme peut s’avérer valable pour des processus standardisés et robustes, mais rarement pour des machines spéciales.
Pourquoi de telles situations ? Les raisons sont multiples. Voici quelques explications :
- Une confiance excessive dans la technologie de la part des équipes R&D et méthodes industrielles.
- Une analyse de la demande client et de la conception du produit insuffisamment approfondie, systémique ou réfléchie, souvent orientée vers une solution technologique plutôt que vers une approche Lean Design.
- Un demandeur laissant trop de latitude au fournisseur d’équipements, qui reste enfermé dans ses paradigmes de conception.
- Un cahier des charges pas assez précis plaçant le demandeur dans une position de faiblesse avec peu de marge de manœuvre pour piloter le fournisseur.
- Un processus d’étude et de rédaction du cahier des charges non partagé avec les acteurs principaux (production, utilisateurs, maintenance, qualité, etc.).
Comment procéder ? En appliquant les principes Lean à la conception des équipements, nous pouvons répondre aux questions suivantes :
- Comment gagner en flexibilité face à l’évolution constante des exigences clients ?
- Comment augmenter la disponibilité des machines nouvelles ou existantes ?
- Comment réduire les coûts tout en améliorant la productivité, la qualité, la sécurité et la satisfaction client ?
Pour être compétitif, il est essentiel que les équipements soient conçus pour offrir des performances optimales et améliorer vos indicateurs de qualité, coûts, délais et bien-être des personnes (QCDP), tout en maximisant les marges bénéficiaires. Il est donc primordial de concevoir des machines plus flexibles, plus sûres et plus fiables, pouvant s’intégrer facilement aux systèmes existants.
Lean design ou comment appliquer les principes Lean pour optimiser la productivité et la qualité dès la conception :
- Intégrer la sécurité et l’ergonomie dynamique.
- Appliquer les principes Lean à la conception des machines :
- Comprendre et analyser la valeur client.
- Chasser les gaspillages selon les principes Lean.
- Analyser les processus selon les besoins (VSM).
- Simplifier et standardiser les conceptions (DfM/DfA).
- Intégrer le Juste-à-Temps rythmé par le Takt Time.
- Appliquer les principes d’auto-qualité : isoler les défauts pour éviter leur transmission.
Mettre en place la TPM (Total Productive Maintenance) pour garantir fiabilité et interventions simplifiées :
- Accès facilité pour le nettoyage, le changement d’outils et la maintenance.
- Identification visible des éléments et composants de sécurité.
- Maintenance de niveau 1 et 2 sans outils spéciaux ni déplacement d’équipement.
- Acheminement des câbles en conduit ou tube.
- Liste des pièces de rechange classées par criticité.
- Concevoir des machines modulaires pour maximiser la flexibilité.
- Réaliser des itérations courtes (approche MVP) lors des validations de conception.
- Effectuer une analyse AMDEC (Analyse des Modes de Défaillance et de leurs Effets).
- Installer des Poka Yokes selon le plan de contrôle.
- Tester et valider en groupe pluridisciplinaire (prototypes virtuels, maquettes à l’échelle 1, etc.).
- Rédiger un cahier des charges fonctionnel très détaillé.
Et très important, il est important de travailler en mode projet et en mode chantier de type Kaizen pour mobiliser l’ensemble des personnes concernées « concepteurs, méthode industriel, technicien de maintenance, qualité et les utilisateurs en production)
Si ce sujet vous intéresse, nous proposons une formation-action sur la conception Lean des machines et lignes de production, ainsi qu’un processus chantier Kaizen dédié au Lean Design.